Introduction
Diesel generators play a crucial role in providing backup power during emergencies and in areas where access to the main power grid is limited. These generators are relied upon by various industries, businesses, and households to ensure uninterrupted power supply. However, the performance and longevity of diesel generators are heavily dependent on the quality of the fuel used. In this article, we will explore the importance of fuel quality standards for diesel generators and the implications of using substandard fuel. We will also discuss the key parameters that define fuel quality and the measures that can be taken to ensure optimal performance of diesel generators.
Importance of Fuel Quality for Diesel Generators
Fuel quality is a critical factor that directly impacts the efficiency, reliability, and longevity of diesel generators. The combustion process in a diesel engine is highly sensitive to the quality of fuel being used. Poor-quality fuel can lead to incomplete combustion, increased emissions, reduced engine performance, and increased maintenance costs. In extreme cases, the use of contaminated or low-quality fuel can cause catastrophic engine failures, resulting in costly repairs and downtime.
The importance of fuel quality for diesel generators can be understood by considering the following key factors:
1. Combustion Efficiency: High-quality diesel fuel is essential for ensuring proper combustion within the engine cylinders. Proper combustion results in optimal power output, fuel efficiency, and reduced emissions. Poor-quality fuel, on the other hand, can lead to incomplete combustion, causing a buildup of carbon deposits in the engine, which can result in reduced power output and increased fuel consumption.
2. Engine Performance: The performance of a diesel generator is directly linked to the quality of the fuel being used. 500kw diesel generator for oil and gas facilities and high-quality fuel ensures smooth engine operation, consistent power output, and minimal wear and tear on engine components. Substandard fuel can lead to engine knocking, reduced power output, and increased engine wear, ultimately affecting the overall performance and reliability of the generator.
3. Maintenance Costs: Using low-quality fuel in a diesel generator can result in increased maintenance costs over time. Contaminants such as water, dirt, and impurities present in substandard fuel can cause damage to fuel injectors, filters, and other engine components. This can lead to frequent breakdowns, unplanned maintenance, and higher repair costs, significantly impacting the total cost of ownership of the generator.
4. Environmental Impact: The combustion of diesel fuel generates emissions that contribute to air pollution and climate change. High-quality fuel with low sulfur content and proper additives can help reduce harmful emissions such as nitrogen oxides (NOx) and particulate matter. Compliance with environmental regulations and standards is crucial for diesel generator operators to minimize their impact on the environment and public health.
Parameters Defining Fuel Quality Standards
Fuel quality standards are established to ensure that diesel fuel meets specific criteria for performance, cleanliness, and environmental impact. These standards are set by regulatory agencies, industry organizations, and fuel suppliers to guarantee the quality and consistency of fuel products. The key parameters that define fuel quality standards for diesel generators include:
1. Cetane Number: The cetane number is a measure of the ignition quality of diesel fuel. A higher cetane number indicates better ignition characteristics, leading to smoother combustion, improved engine performance, and reduced emissions. Fuel with a higher cetane number is preferred for diesel generators as it promotes efficient combustion and reliable starting in a wide range of operating conditions.
2. Sulfur Content: Sulfur content is a critical parameter that affects both engine performance and environmental emissions. High sulfur content in diesel fuel can lead to increased emissions of sulfur oxides (SOx), which contribute to air pollution and acid rain. Low-sulfur diesel fuel is recommended for diesel generators to comply with emission regulations and minimize environmental impact.
3. Lubricity: Lubricity refers to the ability of diesel fuel to provide lubrication to fuel system components such as injectors and pumps. Low lubricity fuel can lead to increased wear on engine components, resulting in reduced efficiency and increased maintenance costs. Diesel fuel with adequate lubricity additives is essential for ensuring the longevity and reliability of diesel generators.
4. Water and Sediment Content: Water and sediment can contaminate diesel fuel and cause corrosion, microbial growth, and filter plugging in the fuel system. Fuel with high water and sediment content should be avoided as it can lead to engine malfunctions and fuel system failures. Regular testing and monitoring of water and sediment levels in diesel fuel are essential to prevent fuel-related issues in diesel generators.
5. Cold Flow Properties: Diesel fuel can thicken and form wax crystals at low temperatures, leading to fuel gelling and filter plugging in cold weather conditions. Fuel with proper cold flow properties, including low cloud point and pour point, is essential for ensuring reliable engine operation in cold climates. Additives such as cold flow improvers can be used to enhance the cold weather performance of diesel fuel.
6. Stability and Storage Life: Diesel fuel can degrade over time due to oxidation, microbial growth, and chemical reactions, leading to fuel instability and poor engine performance. Fuel stability additives can be used to inhibit oxidation and prolong the shelf life of diesel fuel. Proper storage and handling practices, including maintaining clean and dry storage tanks, are essential for preserving the quality of diesel fuel and preventing fuel degradation in diesel generators.
Measures to Ensure Fuel Quality for Diesel Generators
Ensuring fuel quality for diesel generators requires a proactive approach that involves regular testing, monitoring, and maintenance of fuel storage and handling systems. The following measures can be taken to maintain fuel quality and optimize the performance of diesel generators:
1. Fuel Quality Testing: Regular fuel quality testing is essential for verifying compliance with fuel specifications and identifying any deviations from the required standards. Tests such as cetane number, sulfur content, water and sediment content, and cold flow properties should be conducted periodically to ensure that the fuel meets the necessary quality criteria. Testing can be performed in-house using portable test kits or by sending samples to accredited laboratories for comprehensive analysis.
2. Fuel Filtration and Conditioning: Installing high-quality fuel filtration systems in diesel generator fuel supply lines can help remove contaminants such as dirt, water, and microbial growth that can degrade fuel quality. Filtration systems should be properly sized and maintained to ensure efficient removal of impurities and protect the engine from fuel-related issues. Additionally, fuel conditioning equipment such as water separators and fuel polishers can be used to further improve fuel cleanliness and stability.
3. Fuel Additives: The use of fuel additives can enhance the performance and stability of diesel fuel in diesel generators. Additives such as cetane improvers, lubricity enhancers, cold flow improvers, and stabilizers can be added to fuel to improve combustion efficiency, reduce wear on engine components, prevent gelling in cold weather, and inhibit fuel degradation. Care should be taken to select additives that are compatible with the engine and fuel system components to avoid adverse effects on engine performance.
4. Fuel Storage and Handling Practices: Proper storage and handling of diesel fuel are crucial for maintaining fuel quality and preventing contamination. Fuel storage tanks should be clean, properly vented, and equipped with water drains and filters to prevent water ingress and microbial growth. Regular tank inspections, fuel sampling, and tank cleaning procedures should be implemented to ensure that the fuel remains free from impurities and degradation. Additionally, fuel transfer and dispensing equipment should be maintained in good working condition to prevent spills and leaks that can compromise fuel quality.
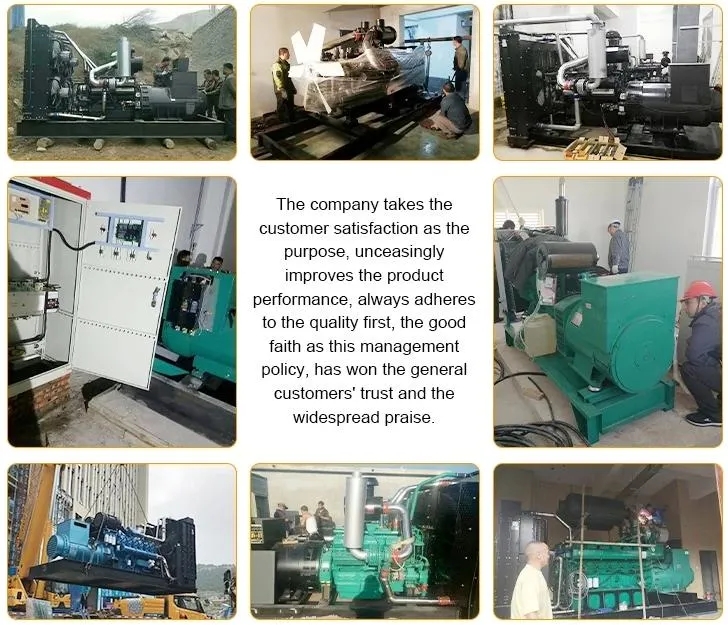
5. Compliance with Regulations: Diesel generator operators should comply with regulatory requirements and industry standards related to fuel quality and emissions control. Regulations such as the Clean Air Act, Environmental Protection Agency (EPA) standards, and fuel quality specifications set by organizations such as the American Society for Testing and Materials (ASTM) should be followed to ensure environmental compliance and safe operation of diesel generators. Regular audits and inspections by regulatory agencies can help verify compliance with fuel quality standards and identify areas for improvement.
Conclusion
Fuel quality standards play a crucial role in ensuring the efficient operation and longevity of diesel generators. High-quality fuel with proper specifications and additives is essential for promoting combustion efficiency, engine performance, and environmental compliance. By adhering to fuel quality standards and implementing proactive measures to maintain fuel cleanliness and stability, diesel generator operators can optimize the performance of their equipment and minimize the risk of fuel-related issues. Regular testing, filtration, conditioning, and storage practices are key components of a comprehensive fuel quality management program for diesel generators. By investing in fuel quality assurance measures, operators can safeguard their investments, reduce maintenance costs, and ensure reliable backup power supply during emergencies.